Semiconductor
It is used to accurately measure the size, shape, and position of semiconductor devices
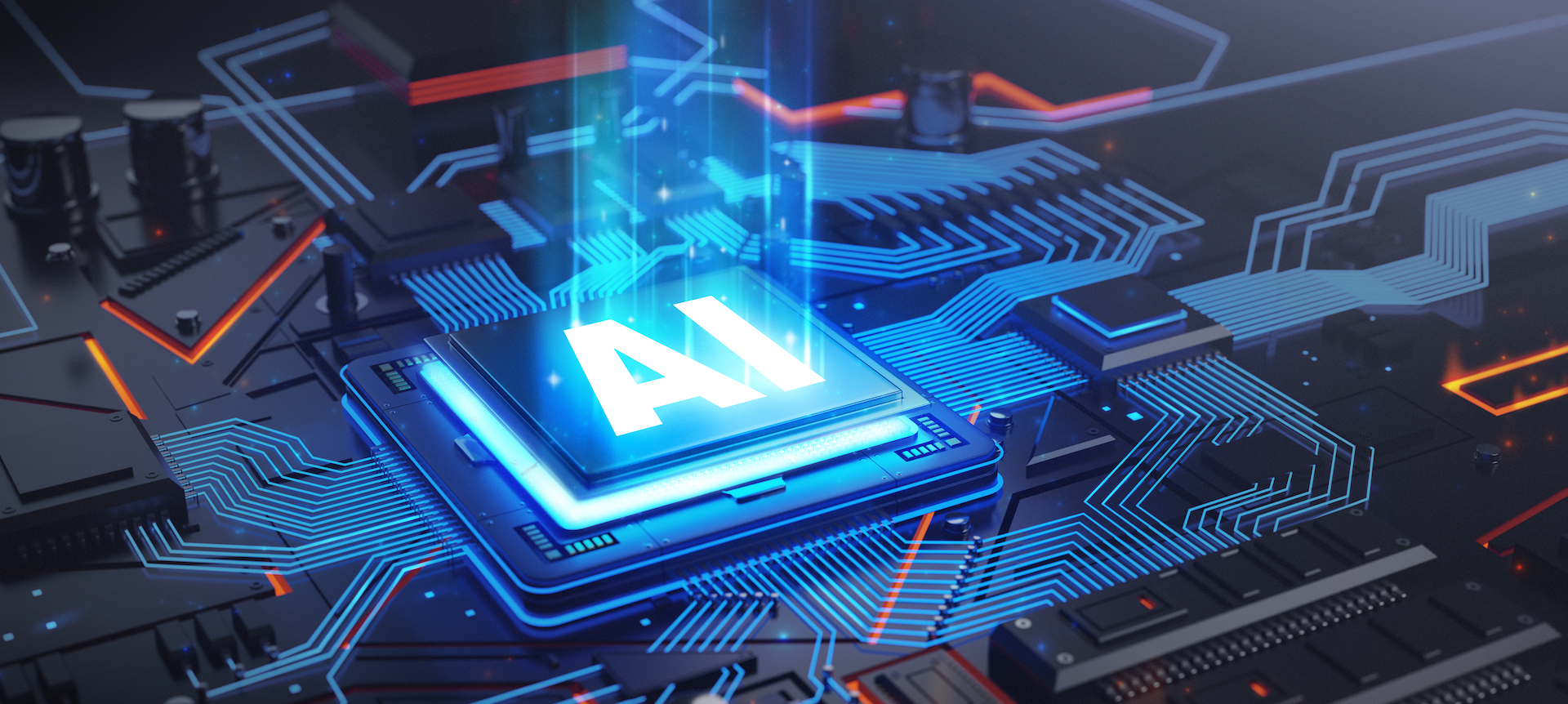
Semiconductor measuring equipment is a variety of equipment used in semiconductor manufacturing and research processes and is used to measure and evaluate the characteristics and performance of semiconductor devices. These equipment play an important role in improving quality, productivity, and supporting research and development processes in the semiconductor industry.
Semiconductor Measurements and Inspection
Measurement
Thin film thickness measurement system SE
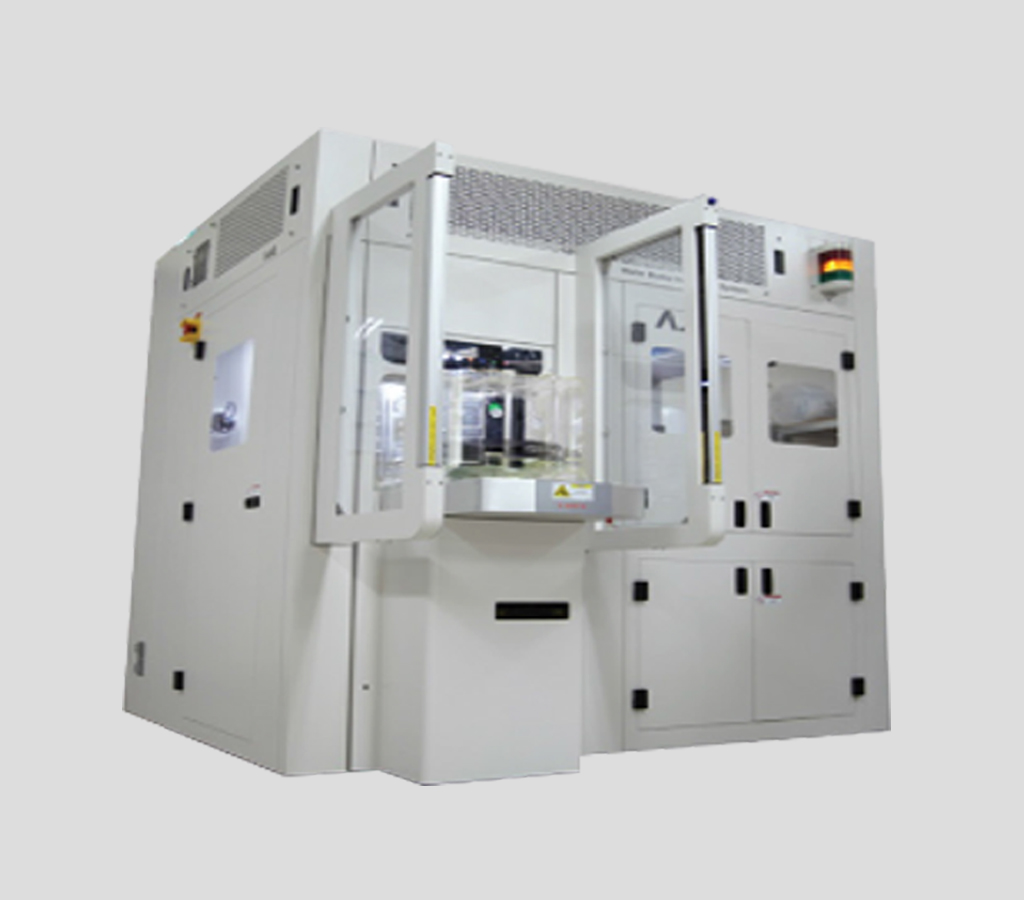
■ Model : AE – 128
• Measurement target: Wafer thin film refractive index & thin film coating thickness measurement
• Measurement item: Thickness measurement of single-layer and multi-layer thin films in the ̊ ~ μm range
• • Beam Diameter : 120μm*300μm
• • Spectral Range : 245nm to 1000nm (Option :~ 1700nm)
• • Fast Camera Sample Alignment
• • UV Spectrometer : 1.6nm pixel resolution, ~ 5nm
• • NIR Spectrometer : – 3.2nm pixel resolution, ~10nm bandwidth (NIR)
• Option: SPC and MES can be linked with internal processes and instruments
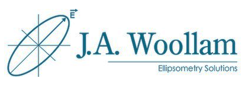
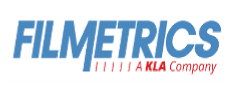
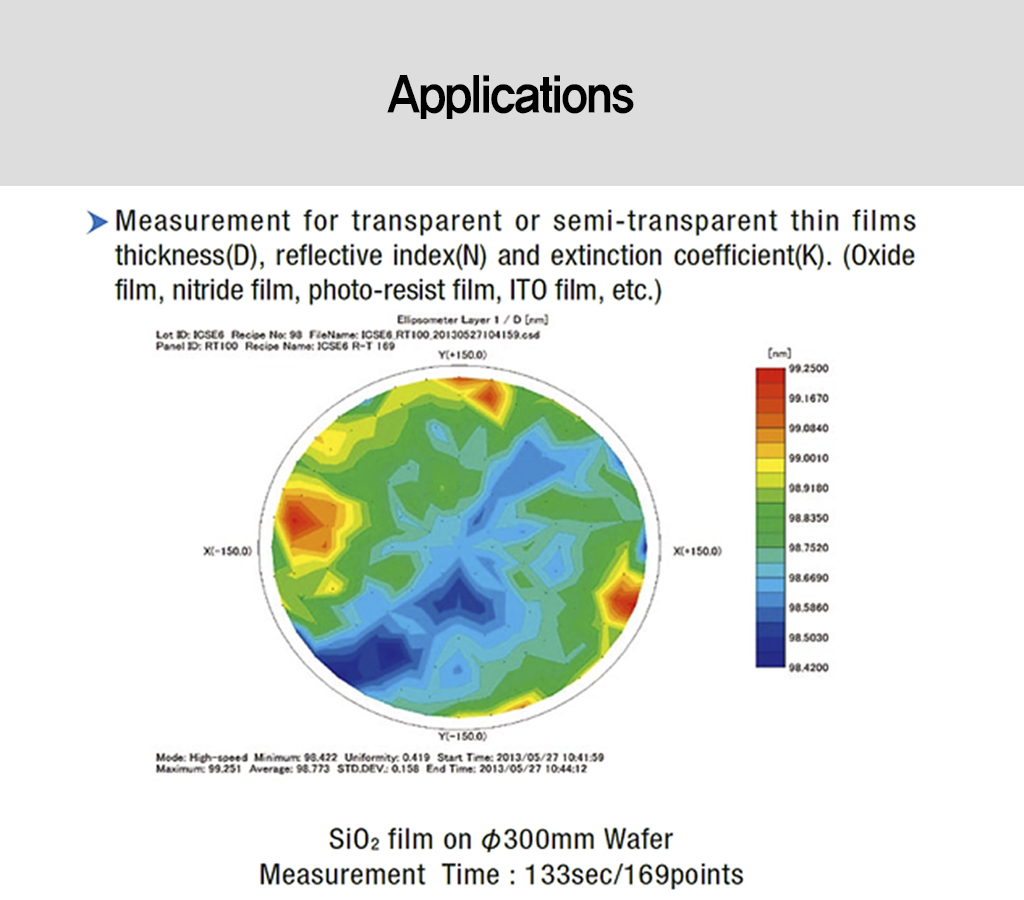
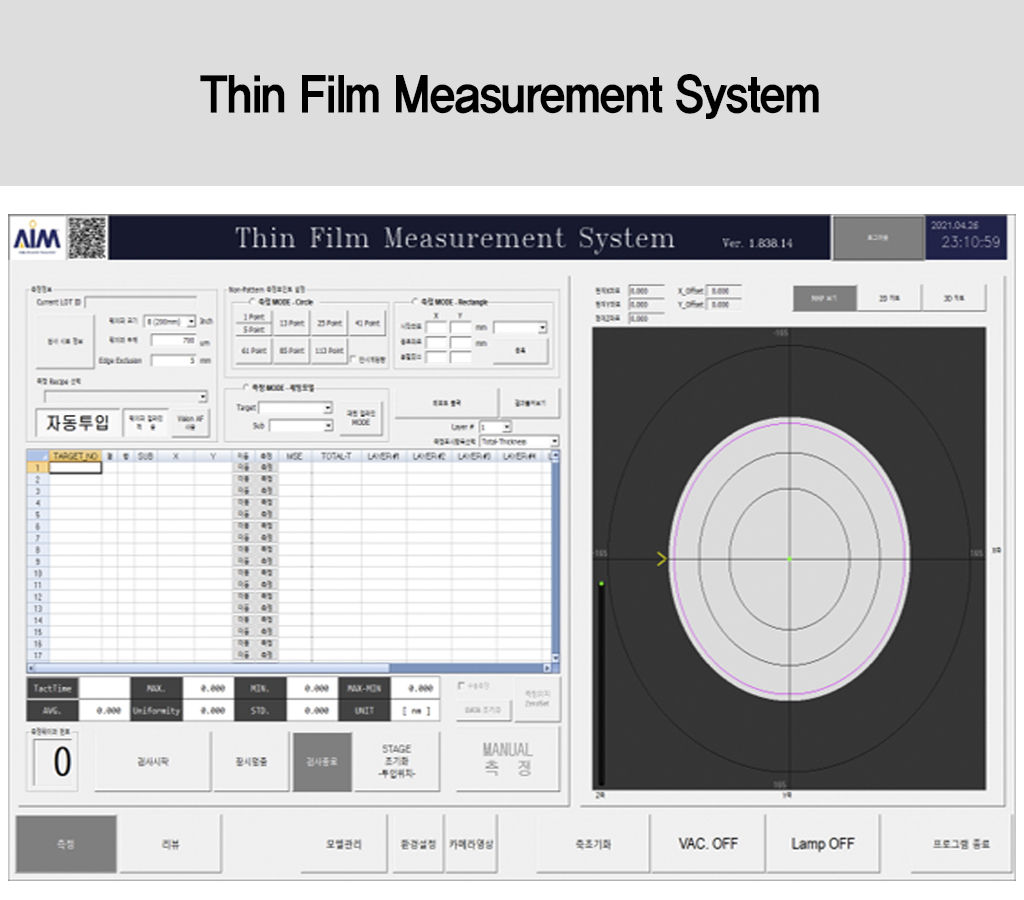
■ Full Auto Mapping Thin-Film Measurement System (Ellipsometer or Reflectometer)
Measurement
Metal Thin Film Measurement System
■ Micro XRF System
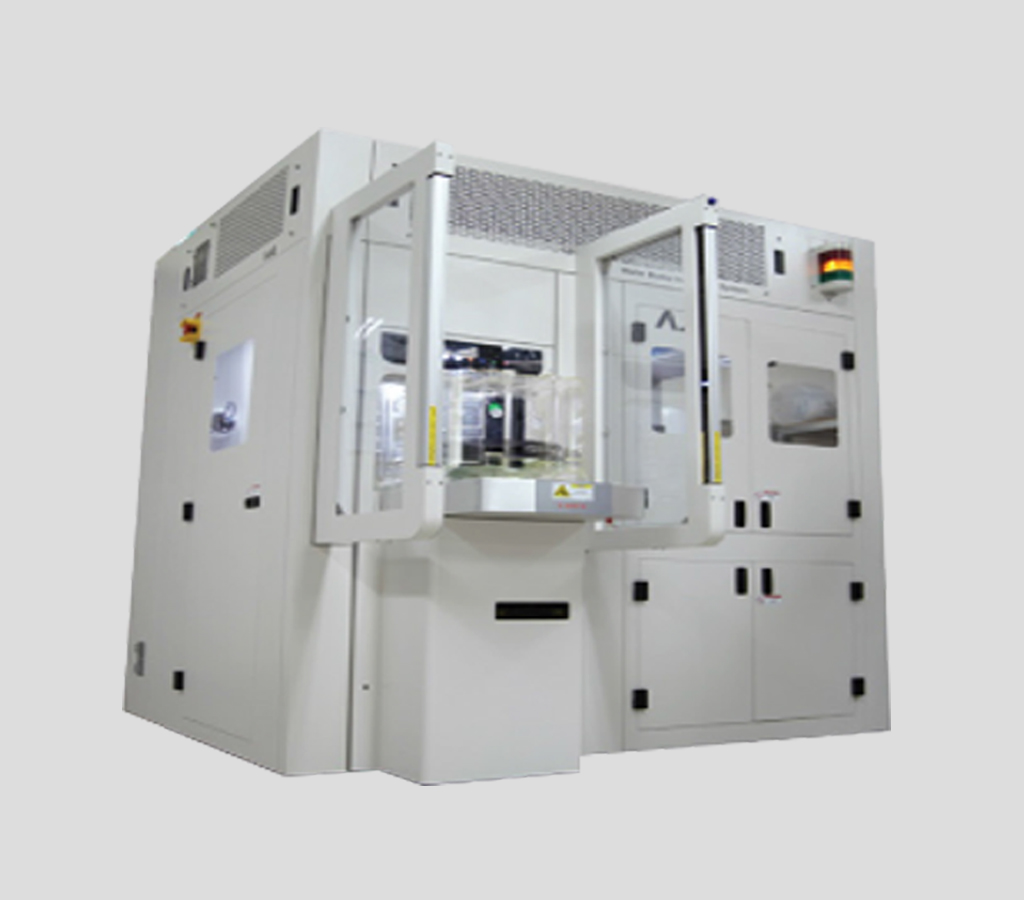
■ Model : AX – 128
- • Measurement target: Wafer’s metal thin film, plating, coating thickness measurement, material composition ratio measurement
• Measurement items: Measurement of a total of 5 layers (10 elements in each layer) including material, 25 elements simultaneously
• Wafer size: 4 to 12 inches
• X-ray : 50W Mo target with Capillary Optics
• Beam spot size: 7.5um FWHM
• detector : Larger Window, 70mm2, high flux SDD with 135eV resolution
• focal length: ~0.5 mm (0.02 inch)
• Video magnification: Macro – 45x (5x digital zoom)
Micro – 150x
• Option: SPC and MES can be linked with internal processes and instruments
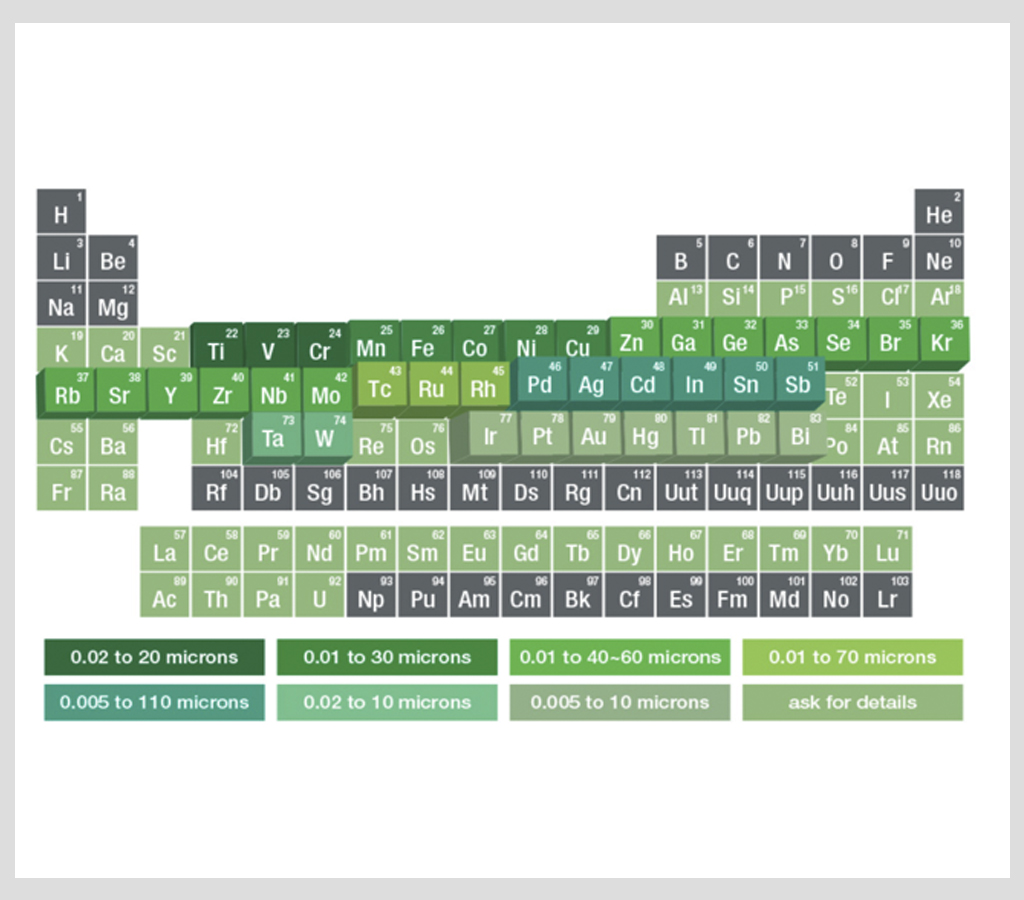
The plating thickness of Au, Ni, Sn, SnAg, Cu, and other metals with a diameter of 30 μm coated on wafer pads, solder bumps, or SMD can be accurately measured.
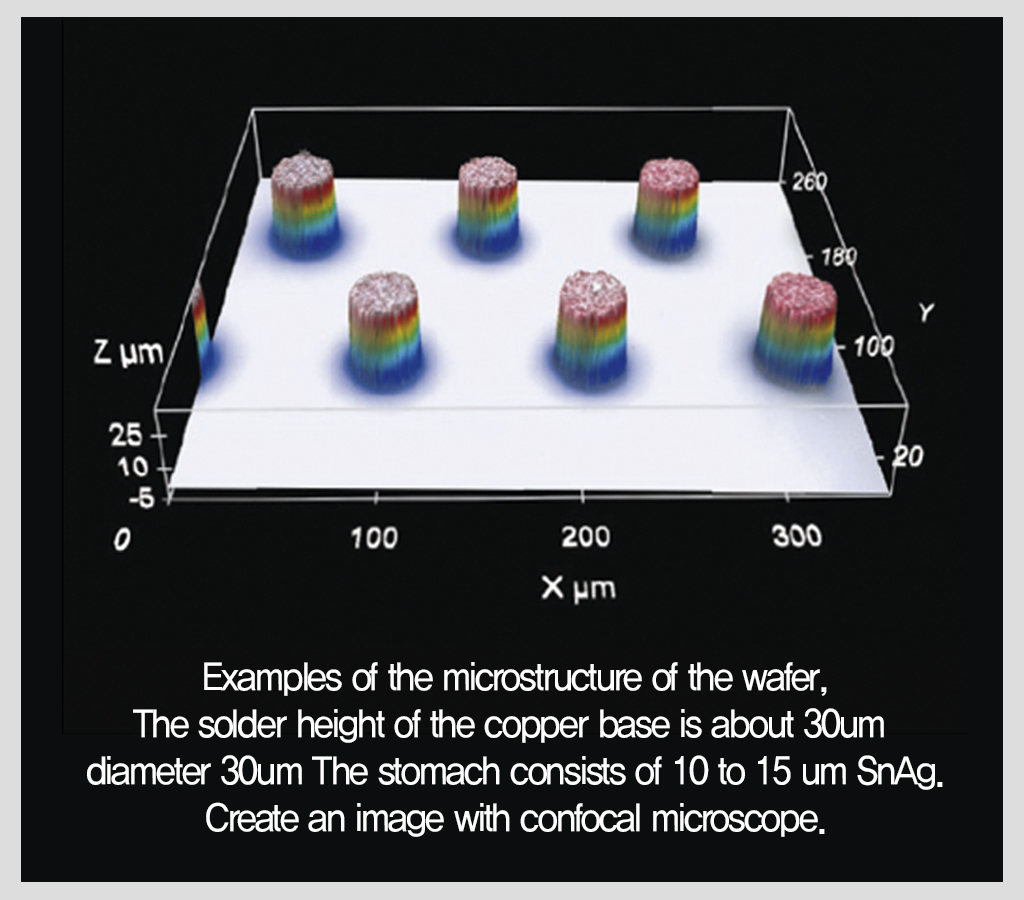
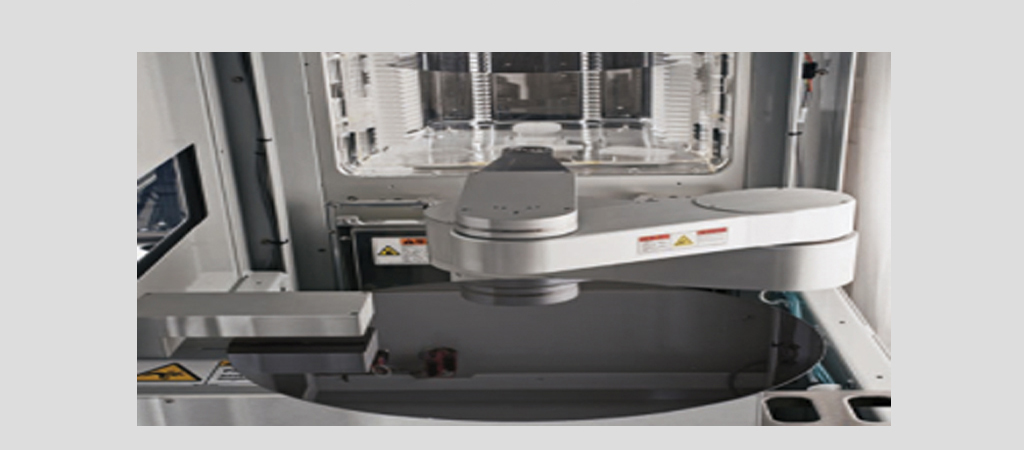
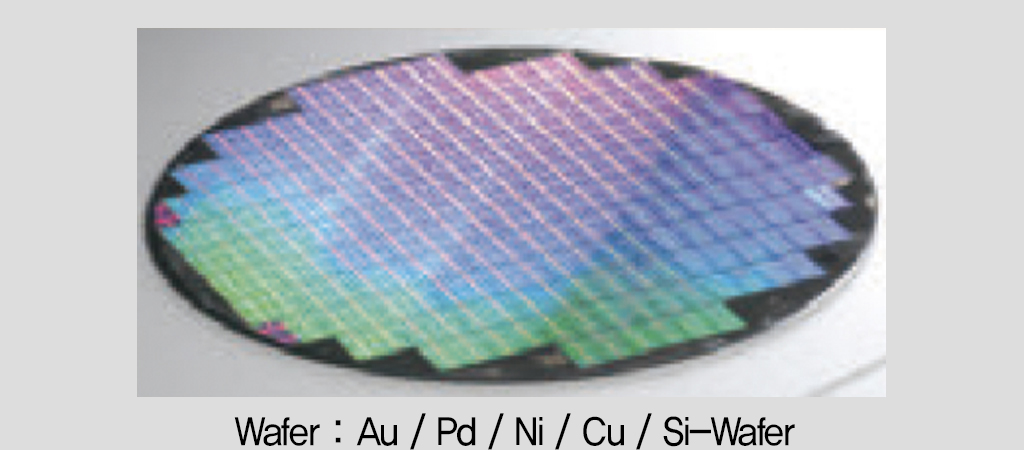
■ Micro XRF System

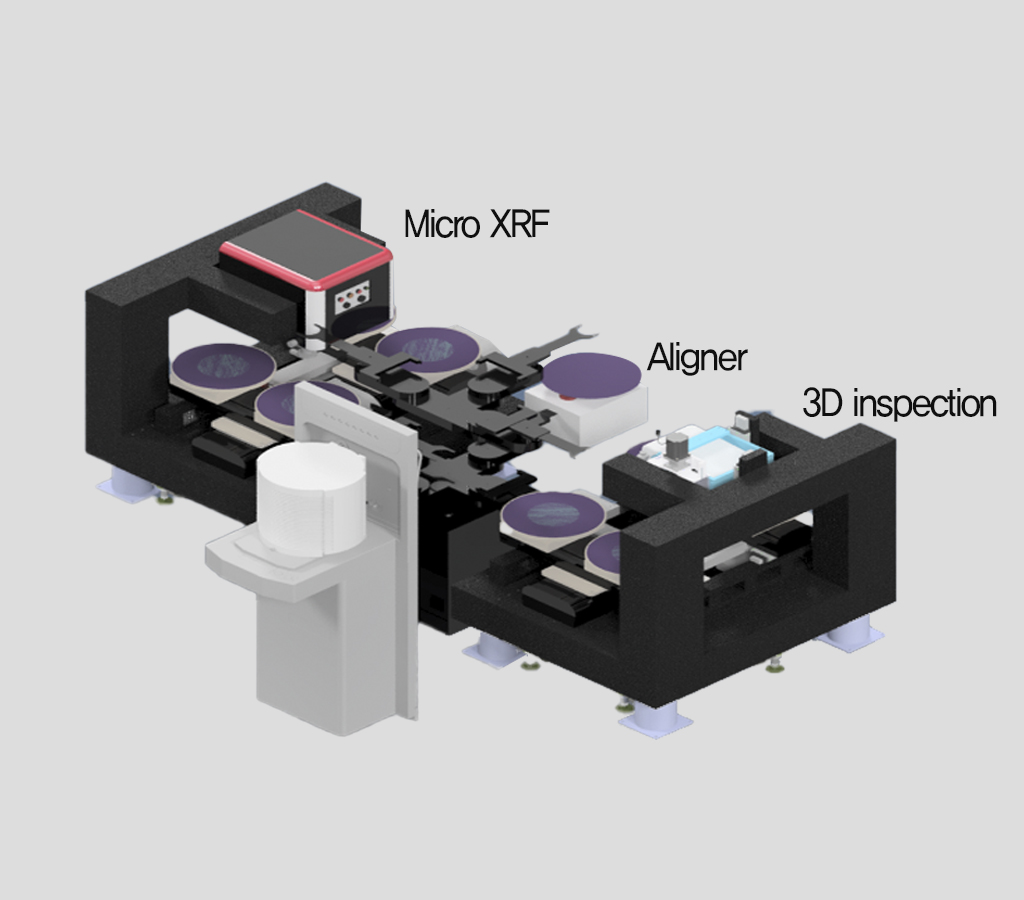
Semiconductor
Semiconductor-Wafer surface inspection
■ Deep Learning - Wafer inspection System
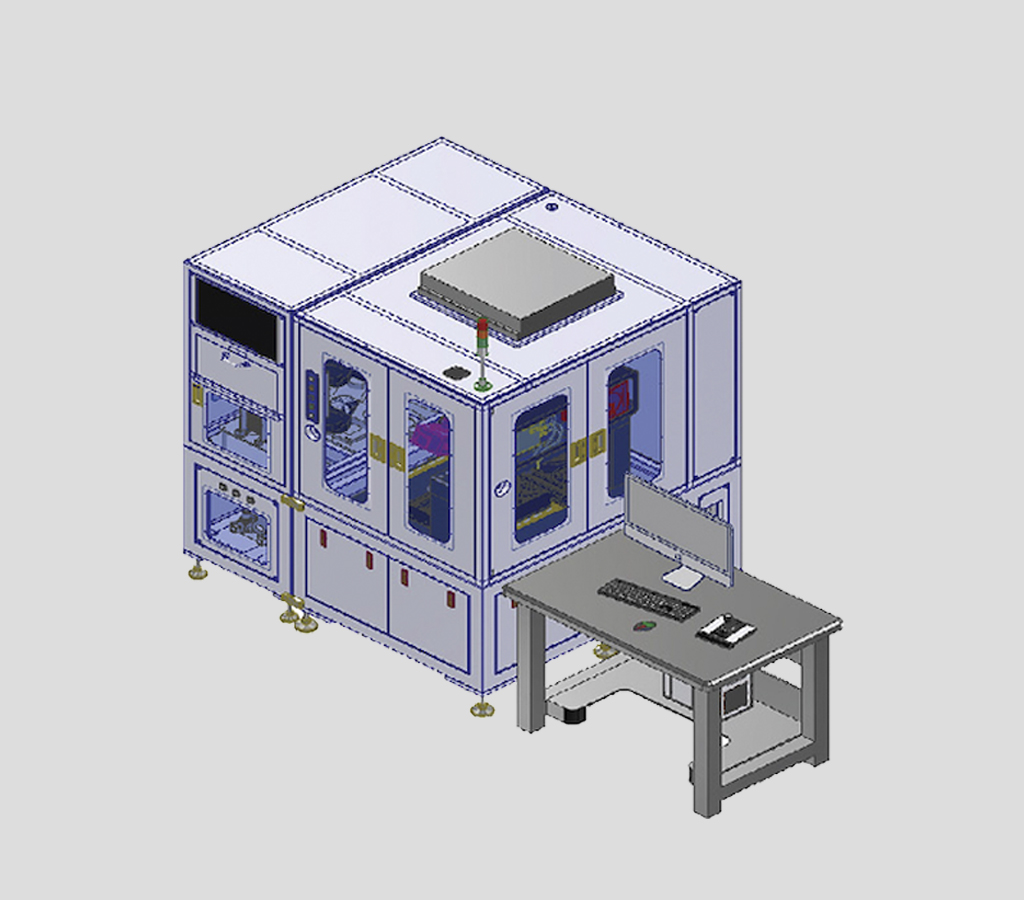
– Best abrasive, stain detection using 360-degree multi-lighting and image processing technology
Result (optical filter treatment only)
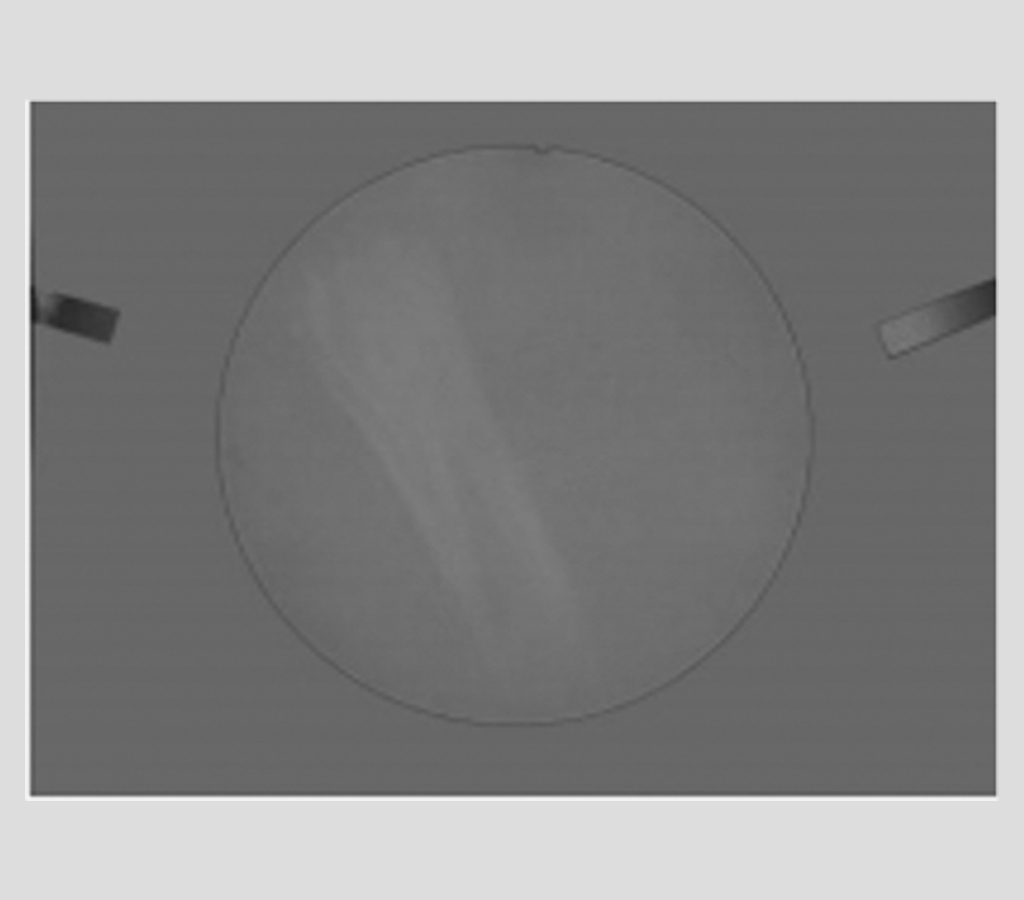
Result (optical filter treatment only)
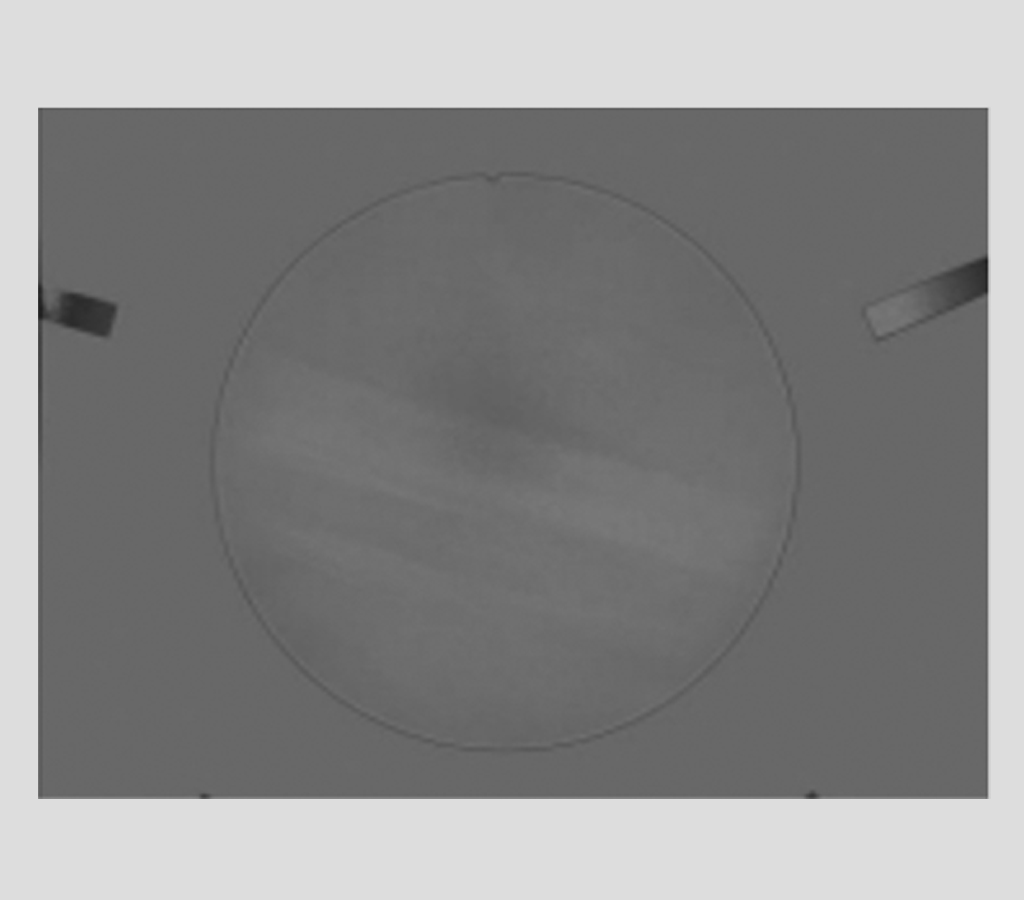
After_Processing
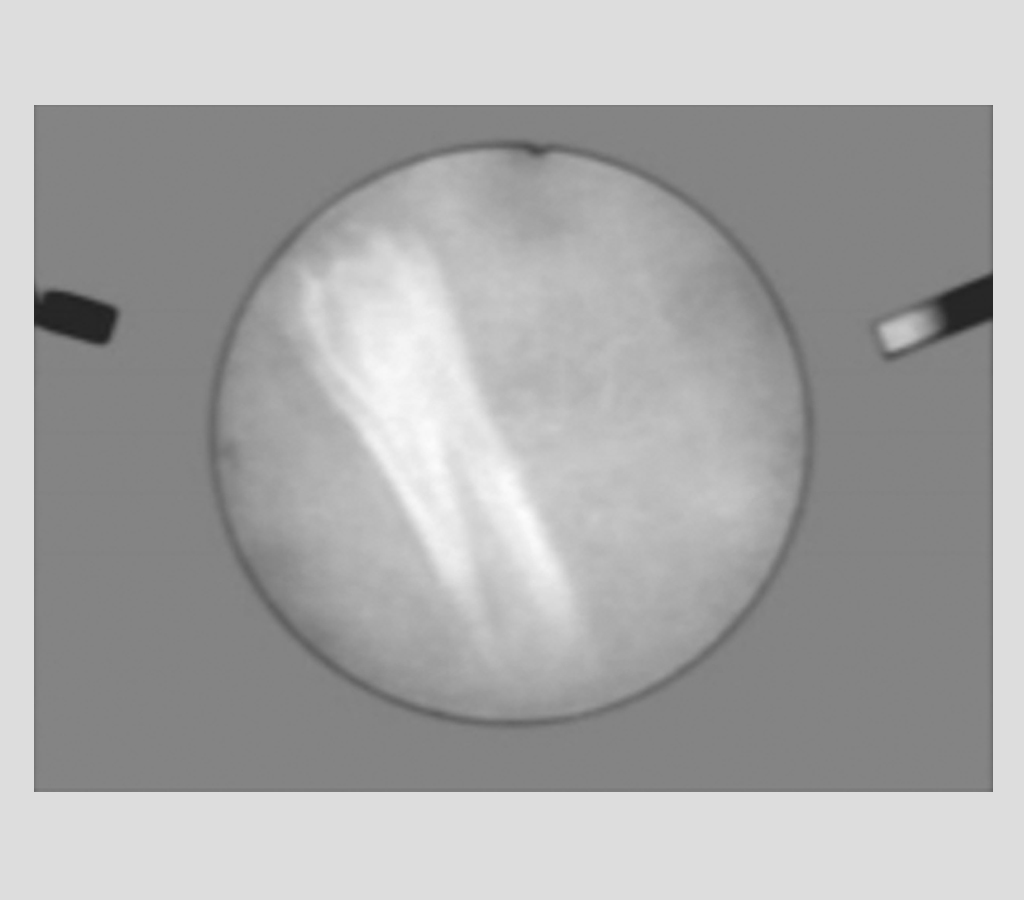
After_Processing
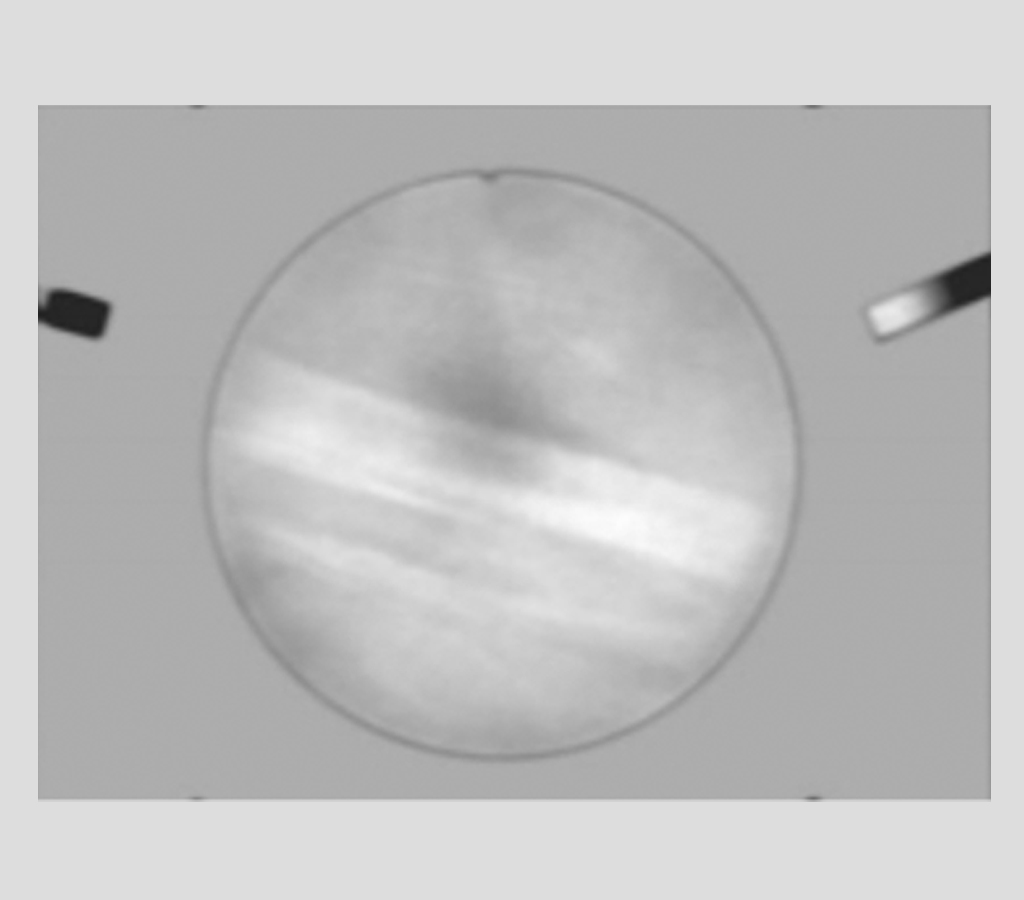
– 360 degrees Free illumination & Surface Property imaging
Just one sensor can do the inspections impossible so far
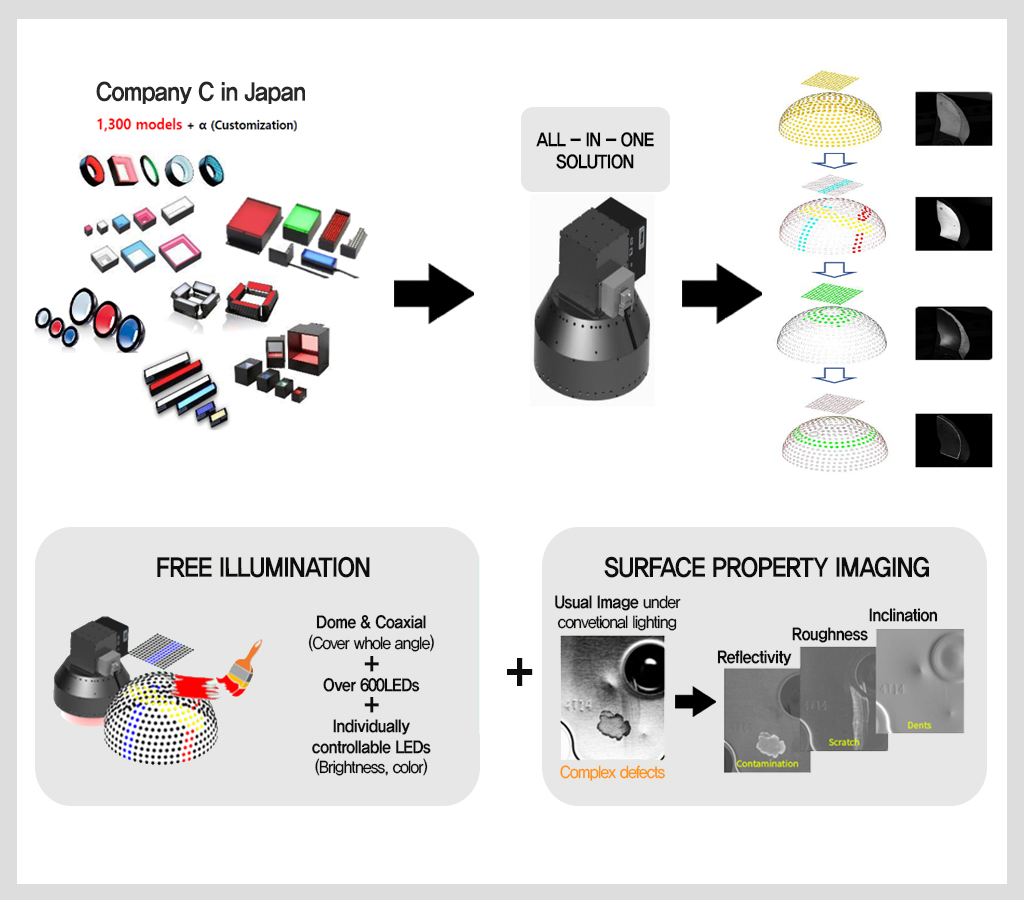
Semiconductor
Semiconductor-Wafer measurement
■ Monitoring wafer Bow, Warp, TTV and Thickness measurement
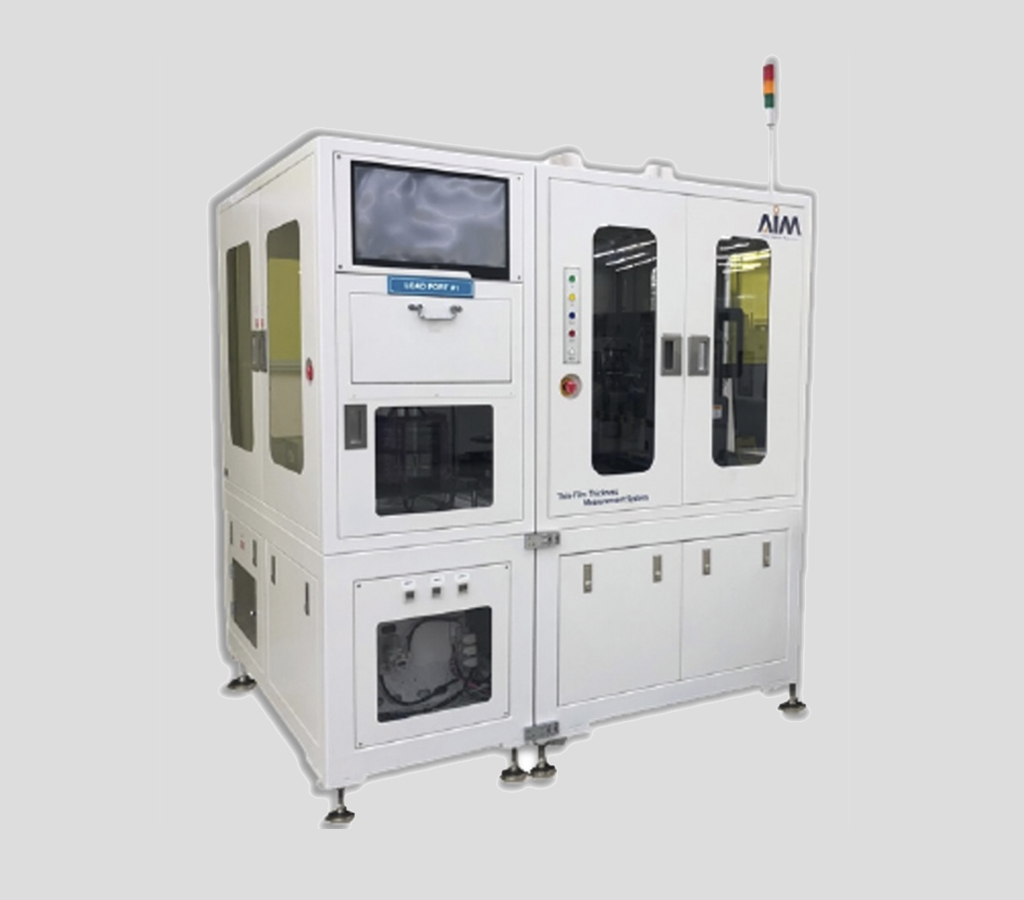
■ Characteristics
Characteristics
• Applied wafer: 6/8 inch wafer
• Applied cassette: 6,8 inches
• Drive Stage: X:350, Y:350
• Wafer seating: Vacuum pad seating
• Loadport: Front
• Aligners: Center alignment & notch alignment
• Robot: Wafer Transfer Robot (Dual)
• a mapping system.
• Navigator Map Features
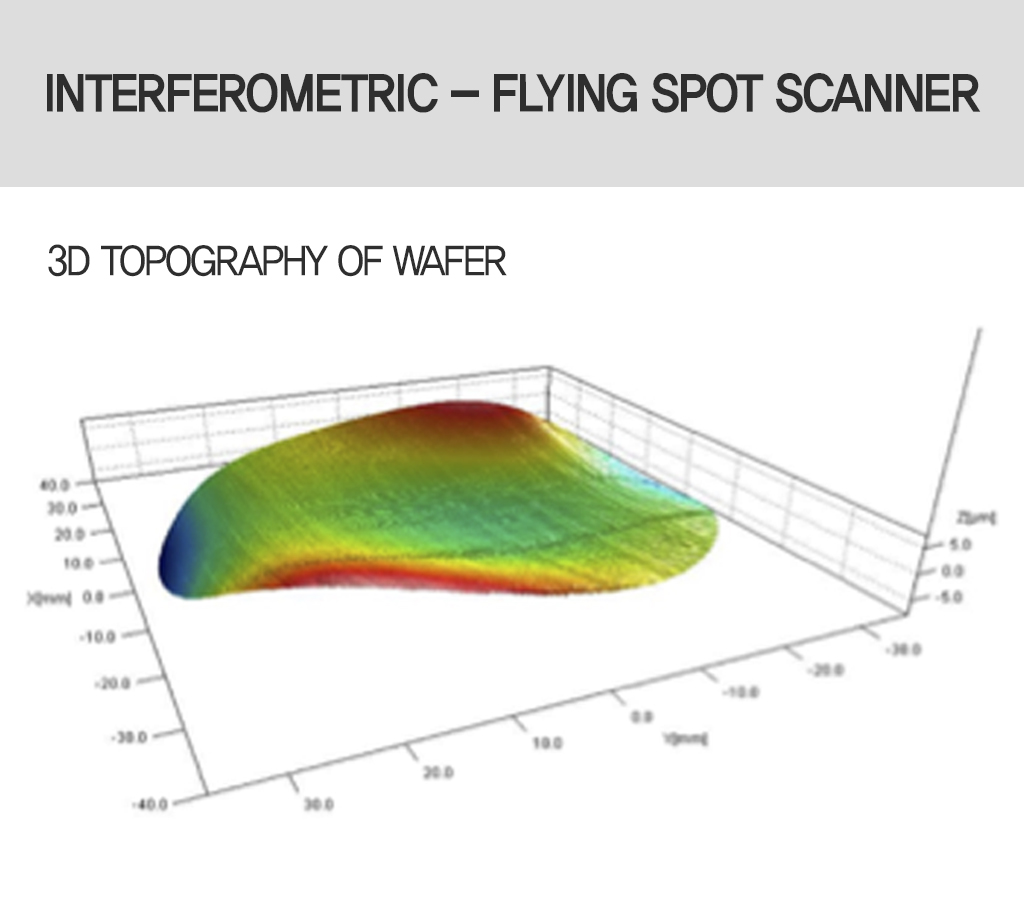
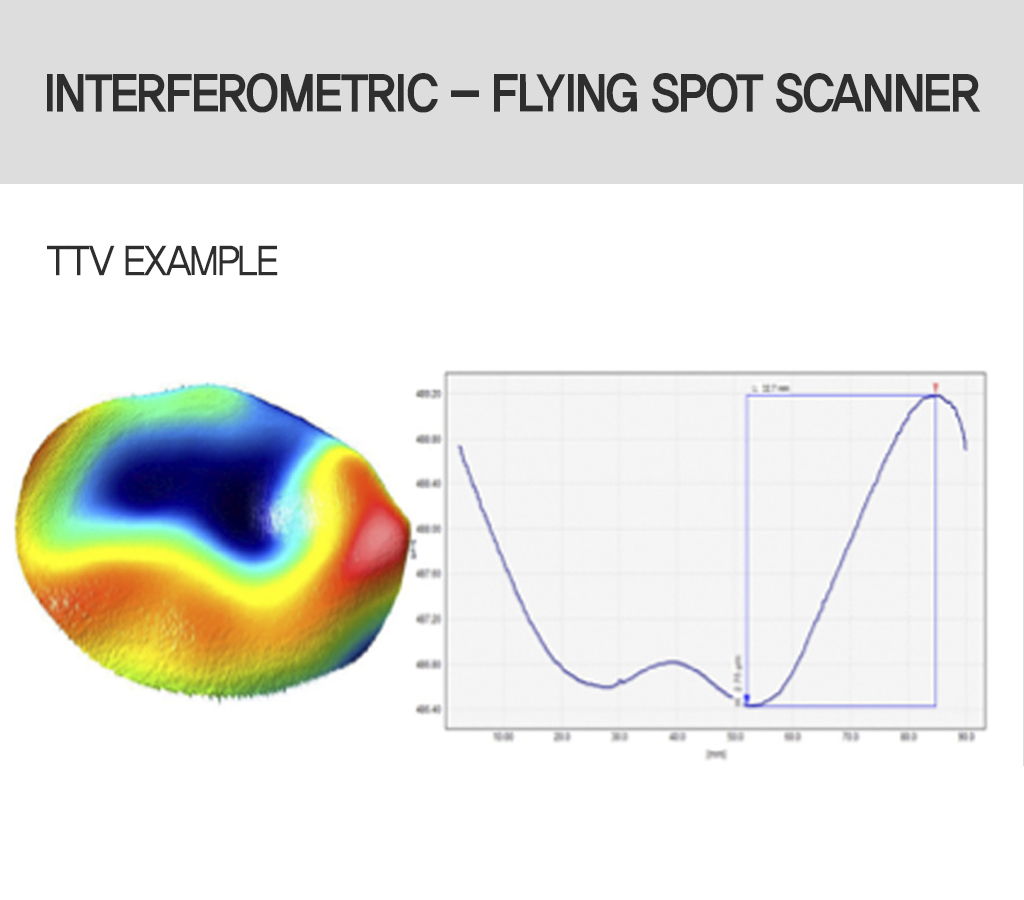
■ 3 TECHNICAL SPECFICATIONS OF FLYING SPOT SCANNER
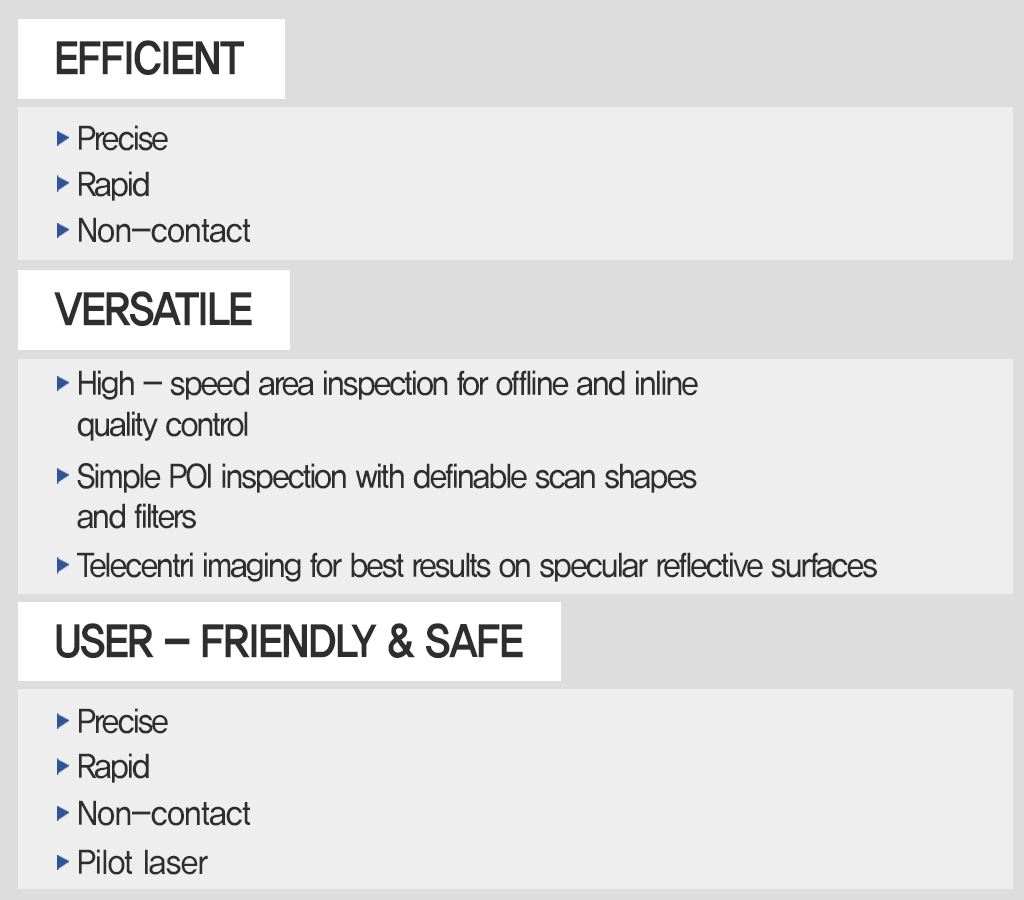
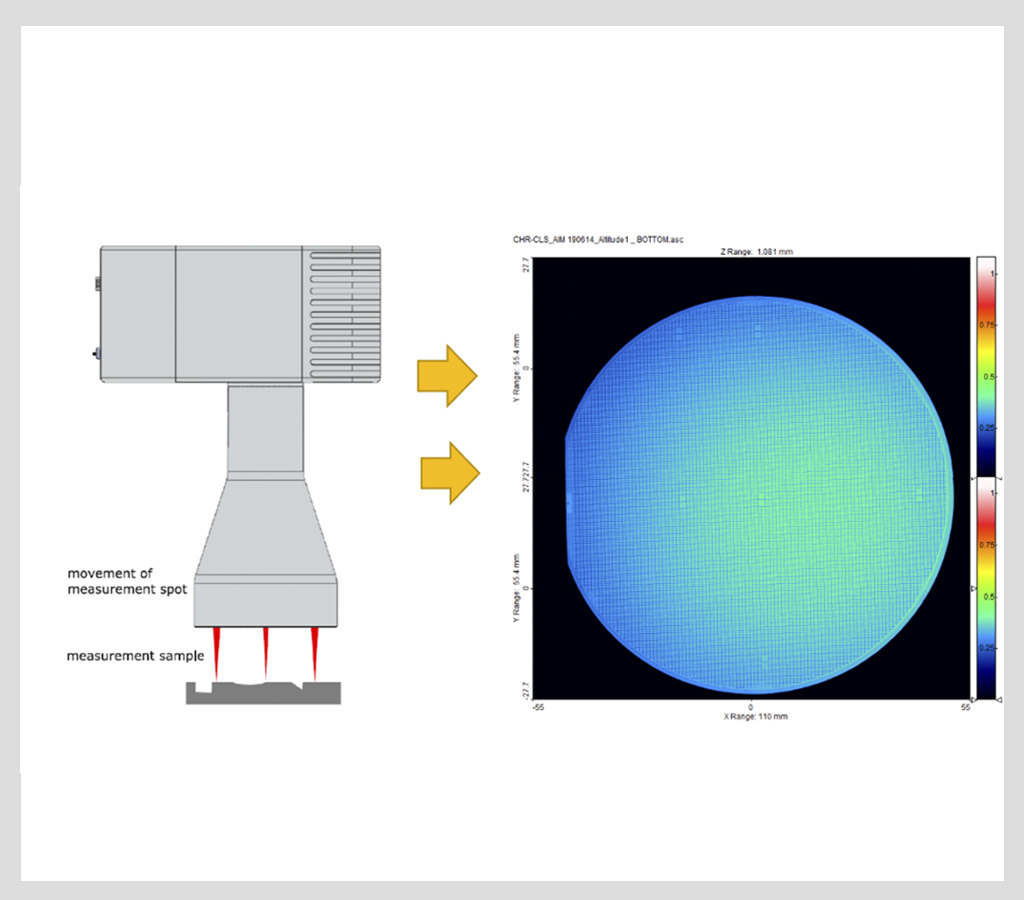
■ Specification
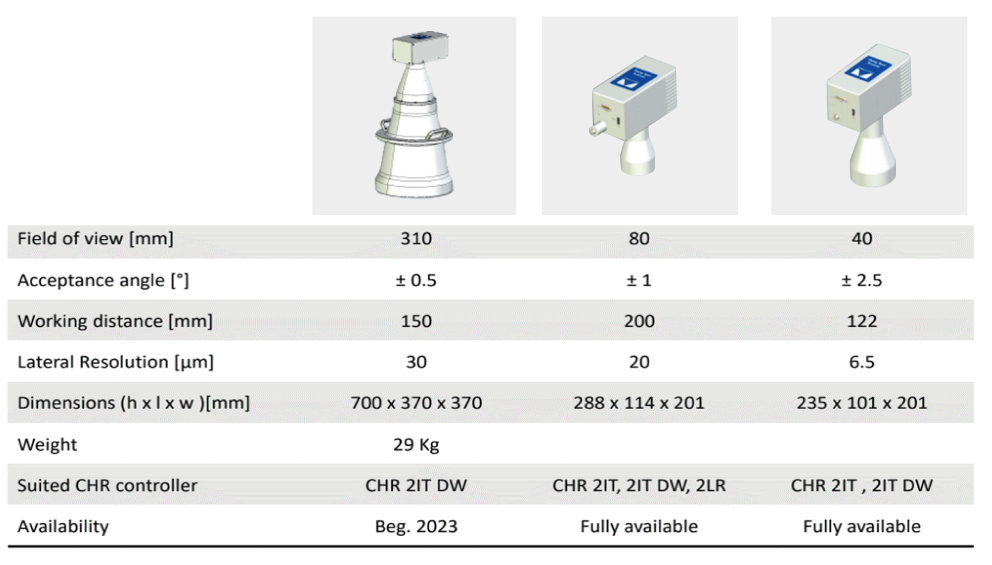
Semiconductor
Semiconductor-Wafer thickness measurement
■ NCG thickness meter
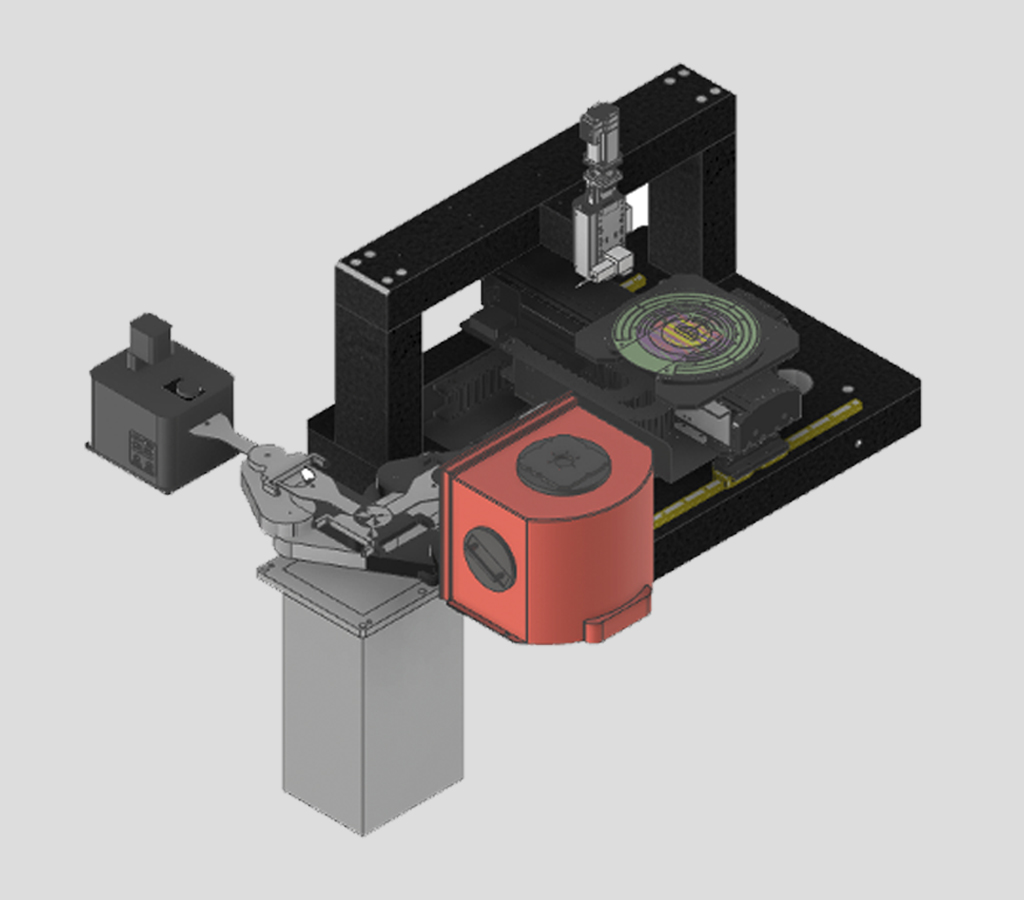
Summary
NCG is a thickness meter based on interferometry technology.
The constant light waves reflected from the layer are separated at the boundary of the object to be measured and measure the thickness of each layer.
NCG is designed to control the thickness of different types of parts such as glass, plastic, and silicon wafers.
Infrared light sources can be used to measure opaque materials. Our gauges show the mechanical cycle time,
Designed to improve and maintain the quality of the final product and to control the process before, during, or after the main stage of work.
NCG is a high-speed precision meter that can interface with any machine for accurate and fast part thickness control.
Within the specified technical specification limits, it can be installed and used inside the fixture or machine, regardless of dry or humid conditions.
Applications
• Various types of silicon. Sapphire wafer thickness measurements
• During process control of background grinding machines and wrapping machines
• Measure each thin or thick layer
• Tape thickness control
advantage
• Ensure part production within target tolerance
• Measurement time optimization
• Guaranteed uniform productivity control
• guaranteed production improvement
• Production history tracking
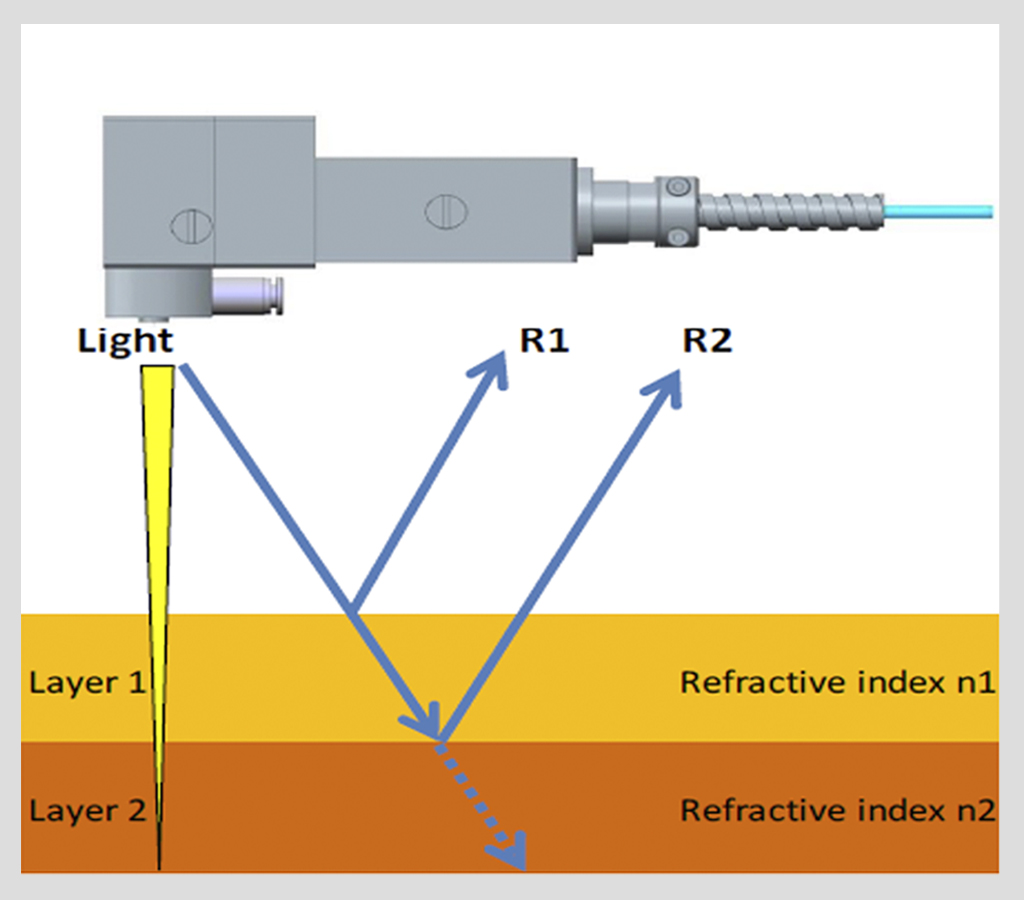
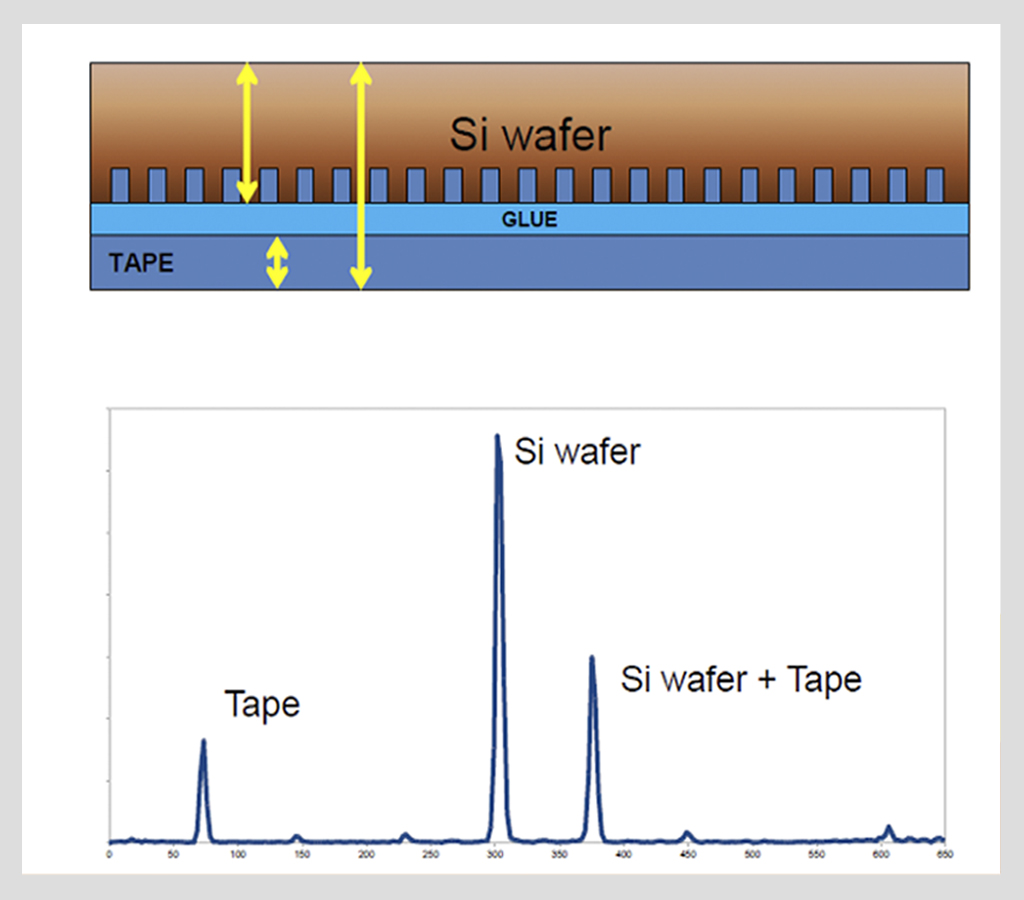
Measurement Principle | Interferometric |
light source | SLED |
Model-specific measurement range* | S1 =37~1850㎛ S2 = 74~3700 ㎛ T1 = 15~900 ㎛ D2 = 60~3000 ㎛ |
Accuracy | ≤ 1㎛ |
axial resolution | 30 nm |
Number of applied channels | 1 |
Interface | Ethernet (10/100 Mbit) RS232 / RS422 as option |
Network Connection | available |
Supply power | 12 ÷ 24 Vtic(+20%/-15%) |
Power consumption | 30 W |
IP rating | IP40 |
Standard IEC 60529 | |
Weight | 2.8 Kg |
Size [mm] | 127 (w)x 129 (h)x 255.5(d) |
![]() | ![]() | |
Measurement Type* | Thickness | |
Distance of Use (WD)** | 1.6,10,100 mm | |
Spot diameter | 18~30 ㎛ | |
azimuth resolution | 9~15 ㎛ | |
angle to the surface | 90º ± 2º | |
fiber optic length | 3/4m | |
fiber optic bending angle | 30mm | |
Protective Fiber | Options | |
IP rating | IP68 | IP40 |
Weight cable excluded | 915g | 80g |
Semiconductor
Semiconductor-Wafer Surface Resistance Measurement
■ Surface resistance, non-resistance measurement
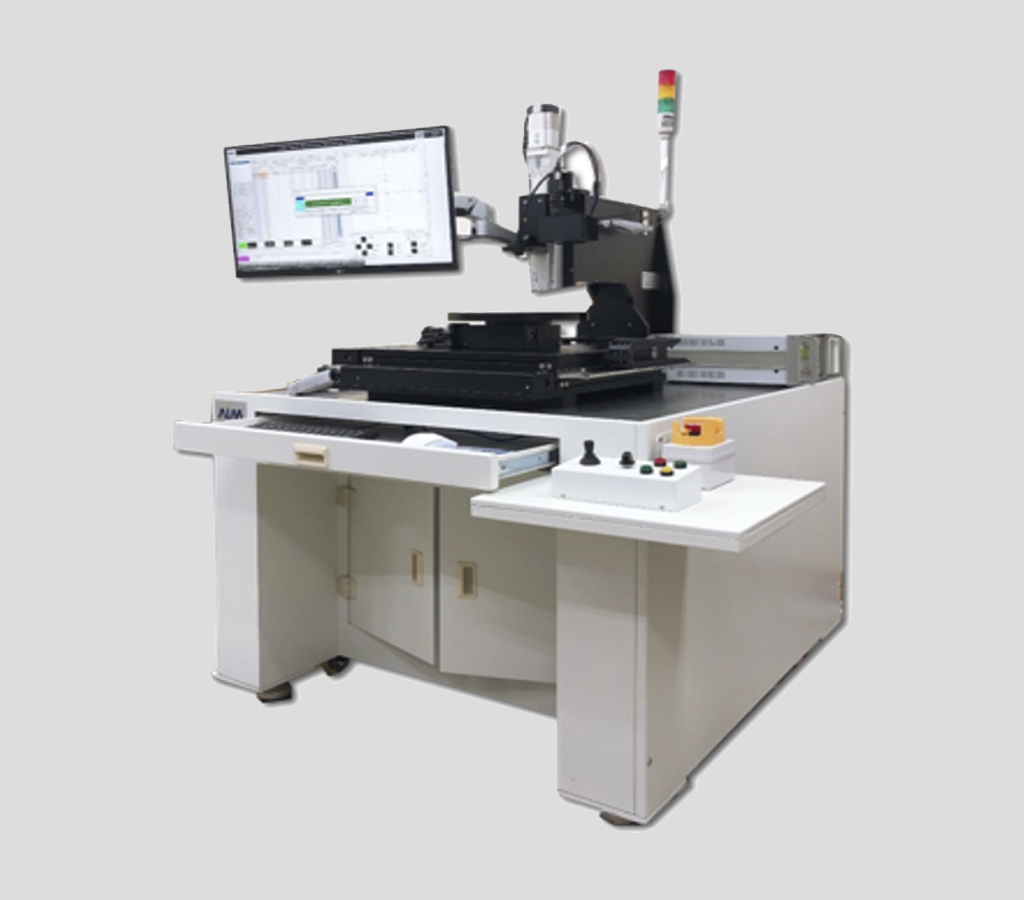
■ Model : AF – 128
• Measure resistance, sheet resistance, non-resistance, conductivity
• Save measurement data (date, sample model, custom selection)
• Repeated measurement for each sample after saving custom points
• Vision Aligner Camera
• • Mapping (Wafer : 0~300mm)
• Measurement range 1mΩ/sq. ~ 1GΩ/sq., 10.0 μΩ·cm to 10.0 MΩ·cm
• 2D, 3D Graphic viewer.
• Option: SPC and MES can be linked with internal processes and instruments
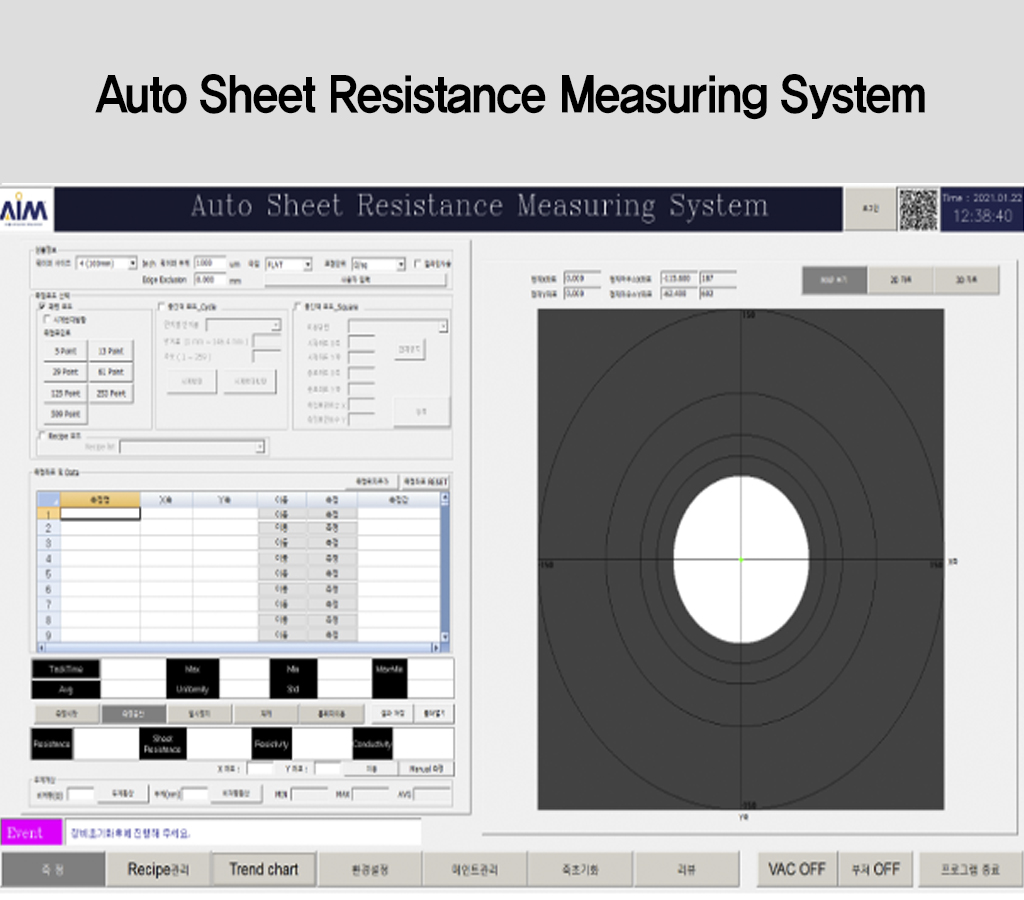
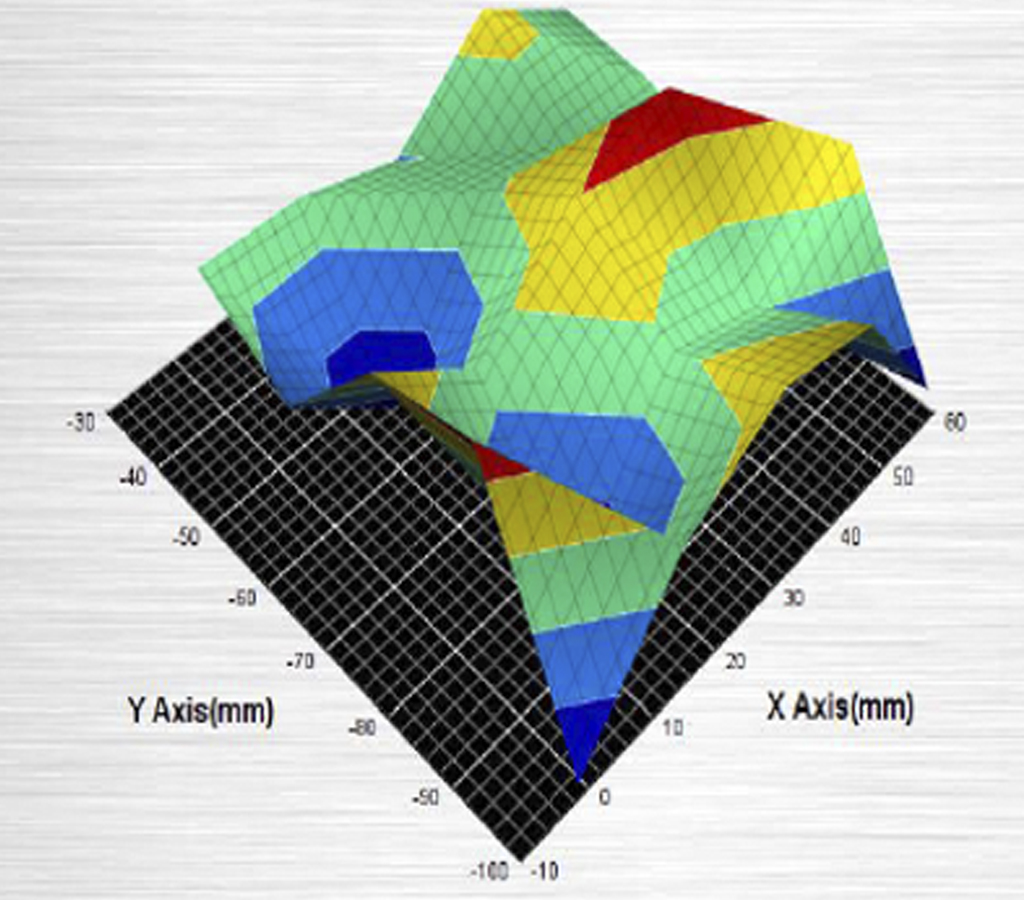
반도체
Semiconductor-Wafer flatness measurement
■ Wafer flatness meter (silicon wafer, sapphire wafer)
• Applied Wafer: 4″ and 6″
• 10 inspection cassettes can be loaded
• 4 bad cassettes can be loaded
• 1 Cycle Time: ~15 seconds (including flatness measuring equipment / measurement time of 5 seconds)
– Measurement data can be determined in real time
• Take a screenshot of the measurement screen and save it to the designated folder
• MES and SPC interlockable